Estimating biofilter size for RAS systems
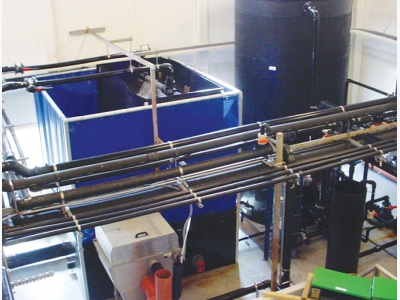
Controlling total ammonia-nitrogen (TAN) concentration is imperative
Trickling filters are simple and robust biological filters that provide nitrification, degassing of carbon dioxide and oxygenation in one component. However, due to the low specific surface area of the media, they are generally larger than most modern filters.
The production of aquatic products in land-based systems using tanks and recirculating aquaculture system (RAS) technology continues to expand worldwide. This trend is driven by the need for intensified production practices that utilize and discharge less water.
A description of these technologies can be found in our previous columns in the Global Aquaculture Advocate. While the installment in the July/August 2015 issue described how to determine the recirculated flow required to the biofilter in an RAS, this article focuses on how to estimate the size of biofilter required for a specific application.
Sufficient capacity, feed rates
To size a biofilter for use in an RAS, the primary concern for the designer is to provide enough biofilter capacity to control the total ammonia-nitrogen (TAN) concentration in the culture tanks to a preset upper limit. Knowing this concentration is very important, as the removal rate of a biofilter is related to the concentration of ammonia-nitrogen available to the bacteria in the filter.
The lower the limit of the TAN concentration selected by the designer, the lower the removal rate will be for a biofilter. The result will be the requirement of a large biofilter for a given application.
Also critical to the process of sizing a biofilter is specifying the maximum feed rate for the system. The ammonia-nitrogen production rate can be estimated based on the rate of feed addition and the protein content of the feed used within the system.
Determining VTR
The biofilter media of this moving-bed reactor initially looks white and floats readily.
The May/June 2015 column noted that the best way to size the nitrification capacity of a biofilter was by determining the volumetric TAN conversion rate (VTR) of the biofilter media in units of g TAN/m3/day. It is critical that the designer under.stand the conditions under which this VTR is determined and compare them to those found within the RAS in question under peak loading periods.
Remember, the lower the TAN concentration going into a biofilter, the lower the VTR for that filter will be. This is the most difficult part of sizing a biofilter for a particular use and, in most cases, is based on previous experience with a given biofilter media in a specific biofilter configuration.
Sizing steps
Thus there are four steps in sizing a biofilter for a particular use in recirculating aquaculture production systems:
- Identify the maximum allowable TAN concentration within the culture tank.
- Estimate the maximum feed rate for the system and calculate the maximum rate of total ammonia-nitrogen generation.
- Determine from previous experience or manufacturers’ specifications the VTR for the biofilter media being used.
- Calculate the estimated biofilter media volume requirement.
Biofilter sizing example
After four months, the “seasoned” media looks brownish and has less buoyancy.
In an example, consider a freshwater RAS operating at a water temperature of 25° C, and assume there is no oxygen limitation, as the dissolved-oxygen concentration of the water is above 4 mg/L to the biofilter. Further assume that the pH and alkalinity of the system are 7.2 and 100 mg/L, respectively, and the maximum desired TAN concentration is 2 mg/L. Additionally, assume the maximum feed rate for the entire system on this biofilter will be at its highest at 60 kg/day of 40%-protein feed.
We now need to estimate the rate of TAN generation cre.ated daily by this feed rate. See equation 1 below (from the July/August 2015 Advocate).
Equation 1
TAN produced (kg/day) = 60 kg Feed/day x 40% Protein x
50% Nitrogen wasted x 0.16 g Nitrogen/g Protein x
1.2 g TAN/g Nitrogen
TAN produced = 2.3 kg TAN/day
Note that the percentage of protein and nitrogen wasted in the equation above should be entered as decimal fractions — 0.4 and 0.5, respectively.
Perhaps the most difficult task in this exercise is the third — determining the VTR that will be used. As noted before, this rate is a function of the type of biofilter media selected and the conditions within the system.
The authors’ experience and published research results indicate the VTR for trickling biological filter media with a specific surface area of 200 m2 under the water quality conditions cited above is approximately 90 g TAN/m3/day. Likewise, a conservative estimate of the VTR for media in a moving-bed reactor under similar conditions is 350 g TAN/m3/day. Equation 2 below can be used to estimate the volume of biofilter media needed to convert the TAN produced to relatively harmless nitrate-nitrogen.
Equation 2
Biofilter media volume (m3) = TAN production (g TAN/day) ÷
VTR (g TAN/m3/day)
We can use this equation to calculate the volume of media a trickling filter would need as:
2,300 g TAN/day ÷ 90 g TAN removed/m3/day = 25 m3
If this trickling filter were sized at 2.5 m square, the media height would be 4.0 m. In trickling filter design, there is space both above and below the biofilter media. In all, this trickling filter might be 5.3 m high with 0.3 m available for water distribution above the media and 1 m below the media to collect and direct the water back to the production system.
Likewise, we can calculate the volume of moving-bed media required for the system in this example. That volume is estimated using equation 2 as:
2,300 g TAN/day ÷ 350 g TAN removed/m3/day = 6.57 m3
To allow the media to have room to be mixed with aeration in moving-bed reactor designs, the reactor is designed so the media takes up no more than 70 percent of the reactor volume. Hence, the volume of a reactor with 6.6 m3 of media would be 9.4 m3. If this reactor were 2.5 m in diameter, the volume needed by the media and water would require the height to be 1.9 m. Adding 0.3 m to the reactor for “freeboard” above the water and media, the overall reactor height would be 2.2 m.
Perspectives
From these estimates of biofilter sizing, readers can easily understand why moving-bed reactors have come to dominate the industry. Similar estimates can be made for other biofilter media. However, the designer must have a good idea of the VTR capacity of a specific media under the specific conditions that will be encountered in the commercial production of the aquatic crop planned for the system.
Editor’s Note: This article was based in part on research conducted by the author at North Carolina State University and published in the Volume 23, 2000 Journal of Aquacultural Engineering. The spreadsheet in that publication presents all of what is described here.
Có thể bạn quan tâm

Not all ponds and quarries are suitable for cage culture of fish. Many failures in cage production have occurred because of poor site selection.

Poor water quality that persists for days and weeks is detrimental to crawfish production. Water quality is influenced by many factors, both environmental

Although there are volumes of articles and printed material on the importance of maintaining optimum water quality in aquaculture farming systems