Rising use of automatic feeders in shrimp ponds poses new feed requirements (Part 1)
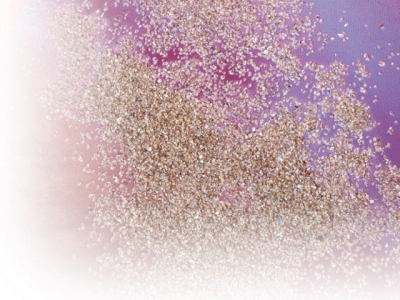
Physical characteristics of manufactured aquafeeds influence performance
The physical characteristics of shrimp feeds largely influence the performance of automatic feeders in shrimp grow-out ponds.
Although the cost of formulated aquafeeds in shrimp farming represents approximately 60 percent of the operating costs, the actual application and distribution of feed in shrimp grow-out ponds is still mostly done manually. This is accomplished by broadcasting the feed pellets from the levees in smaller ponds and from moving boats in larger ponds. However, feeding methods are in continuous development and significant efforts are looking at the automation of these operations.
This is the case of the automatic feeders that have been developed in recent years. Proper use significantly reduces production costs and improve shrimp growth rates. The results obtained show that automatic feeding helps to improve efficiency and profitability in farmed shrimp production.
Several of the factors influencing the performance of automatic feeders are related to the physical quality of the feeds, the mechanics of solids inside the feeder, and the consequences of the radius of range distribution the feed has around the feeder. Added to this is the need for proper training of the staff that manage the feeders and that control the data or systems.
Therefore, it is important to strengthen the physical aspects involved in automatic feeding. These, together with an adequate nutritional quality of the feed, are a decisive combination to maximize the yield and profitability of shrimp farms. This article, (adapted and summarized from the original publication in Revista Acuacultura – Cámara Nacional de Acuacultura, No. 123, June 2018), describes the importance of the physical characteristics of shrimp aquafeeds for use with automatic feeders.
Hoppers and the mechanical behavior of food
The food storage hopper is an essential component in all aquaculture systems with automatic feeding, as its design impacts the performance of the equipment. A continuous and uninterrupted flow of feed ensures that the designed feeding program is executed correctly and the strategy has the expected results.
A common and traditional way of understanding the flow of a solid in a hopper has been based on the application of the angle of repose. This is a useful indicator to know the fluidity of the material: the lower its value, the easier it will be for the feed to flow through. However, while having an impact on the mechanical behavior of solids within the hopper, the angle of repose is not the only factor. The common statement about the fluidity of a material as a direct function of the angle of repose should be avoided, because most solids show different degrees of cohesion.
In short, the behavior of the material depends on the manner in which the force of flow varies with its state of compaction. For example, a cohesive solid can flow and pour through a hole, but after being compressed, the flow will not develop due to the formation of a cohesive arc over the hole. This would suggest that the loading force at the base of the hopper should be minimized and that the hoppers should not be used with feed at maximum capacity.
Coefficient of friction or internal friction
When the surface of the feed or the wall of the hopper is rough, the fluidity decreases due to the occurrence of the so-called anchoring between particles. This, as well as the friction between the feed and the wall of the hopper, lead to the feed eventually not flowing freely.
This in turn can result in a scenario in which the dosing motor continues to operate, but there is no feed dispersion since it is still adhered to the hopper internal walls. The feeding schedule is impaired, particularly during hours when the conditions are the best to feed. Larger particles tend to flow better than smaller particles; therefore, the size of the feed has a great impact on its levels of fluidity inside the hopper.
Flow types in the hopper
Two flow patterns can occur in a hopper: mass flow and central flow (Fig. 1). In mass flow, the entire bed of solids is in motion when the material is discharged from the outlet. This behavior eliminates the formation of stagnant regions and provides a “first-in, first-out” flow sequence, which in turn provides a more uniform velocity profile during operation. A uniform velocity profile also helps reduce the effects of segregation due to differences in solid size.
On the other hand, during central flow only partial sections of the product move, which means that there is no complete discharge of the hopper. In this way, the stationary material of the first batch is left behind and then it will be mixed with the following batches. Central flow is characterized by a condition in which the side walls of the hopper or the bottom walls are too rough for the material to slide.
The hopper in mass flow solves, in a reasonable way, problems such as the irregular or rapid flow of product, variable residence times and the caking with time and in inactive zones. Fig. 1 shows both types of flow. Obviously, it is desirable that mass flow conditions are generated during the discharge of the feeders.
Fig. 1: Illustration of typical mass flow (left) and central flow (right) inside a hopper.
Parabolic movement and radius of feed range
The range (distance) reached by the aquafeed (pelleted or extruded) in an automatic feeder responds to a logic of parabolic movement, with an initial height. In this type of movement, the initial height (distance between the dispensing motor and the surface of the water) plays a critical role in the range reached by the feed.
Theoretically, if we create a table of feed distance ranges for the parabolic movement of an automatic feeder and represent it in an equation, we find that the range Rm depends on the height (Table 1).
Where:
Rm = average radius of range, with Vo = initial velocity
h = height
g = gravity
A reduction in the average radius of the range translates into less space for animals to feed (Table 1). Considering that the feeding areas occupy 3 to 5 percent of the pond area, and that they harbor a large biomass, this reduction is critical – in terms of space – to provide feed for the shrimp. Such a decrease in feeding space could result in competition and promote, intensify and/or enhance territorial behavior.
Molina, feed characteristics, Table 1
Height (m) | Avg. radius of range (m) | Covered area (square meters) |
0.8 | 13.9 | 606 |
1 | 14.08 | 622 |
1.2 | 14.23 | 635 |
1.5 | 14.47 | 657 |
Table 1. Average range radiuses and covered areas for feeders with different heights and at a constant initial velocity.
The physical quality and bioavailability of nutrients are, together, the most important factors to maximize the yield of the feed. The raw material used, as well as the process technology, have a great impact on final feed quality. There are several physical parameters that are measured in a shrimp feed, both in the manufacturing line and in the final product.
Related news

Feeds usually represent 40 to 60 percent of the total production costs in semi-intensive and intensive shrimp aquaculture, so reducing feed-related costs

Commercially produced probiotic strains may provide more support than those found indigenously, but indigenous strains may outperform the use of a non-supplemen

Live colony of macroaggregates and bacteria suspended in the water column can increase survival, feed conversion