Recirculating Aquaculture Systems (RAS)
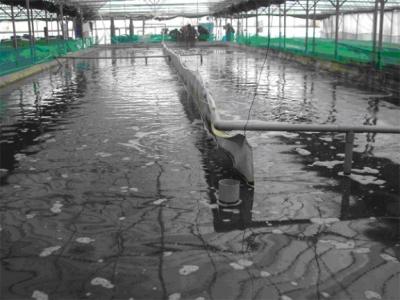
Recirculating Aquaculture Systems (RAS) incorporate additional treatment technologies beyond those used in Partial Reuse Aquaculture Systems (PRAS), allowing for significantly greater quantities of water to be reused. Recirculation systems afford a level of control well beyond any other technology application in aquaculture and provide significant production and economic benefits.
Recirculation systems are usually used where new water supplies are limited or expensive to achieve (i.e. high pumping costs), the risk of introducing pathogens or contaminants into the system with influent water is high, effluent disposal capacity is limited, or where operators want to practice strict control over the water quality and temperature within the fish culture system. Such systems are characterized by increased technical complexity, capital costs, and in some applications, operating costs. However, because RAS allow optimum culture conditions to be maintained year round, independent of fluctuations in water supply quality and ambient temperatures, fish growth rates may be accelerated allowing more fish or larger fish to be produced in the same amount of time. In a well designed system, the production benefits will outweigh the additional costs resulting in a net lower cost of production.
Recirculating Aquaculture Systems maximize water re-use by employing a comprehensive water treatment system. Water treatment processes typically include solids removal, biofiltration, gas balancing, oxygenation, and disinfection. By addressing each of the key water quality concerns through treatment, rather than flushing as is used in flow-through and partial reuse systems, ultimate control over culture conditions and water quality is provided.
Water quality in recirculation systems is highly dependant on the complexity and cost of the water treatment system used. Better water quality may be provided and higher recirculation rates may be achieved through the use of additional treatment processes or with greater intensity of treatment. A typical recirculation system will provide a maximum recirculation rate of 95% – 99% of the system flow rate while maintaining optimal water quality for the fish. However, with the addition of denitrification technologies, and by capturing water extracted from sludge thickening processes, some systems may become effectively “closed” with very little to no exchange of water. A balance must be achieved in design between water quality objectives and treatment system complexity and cost.
Recycling has become an economic imperative in many industries and aquaculture is no exception. Recirculation technology has allowed aquaculture facilities to evolve to meet the growing need for economic and environmental sustainability. PR Aqua is a world leader the large-scale integration of water recirculation and partial reuse technologies in the design and construction of aquaculture facilities. Please contact us to see how recirculation technologies can help you in meeting your production and profitability objectives.
Partial Reuse Aquaculture Systems (PRAS)
Partial Reuse Aquaculture Systems (PRAS) use water treatment processes to allow a portion of the culture discharge water to be recycled and supplied back into the culture tanks. For aquaculture facilities faced with limited water resources, sustainability issues, or a requirement for improved control over culture conditions, reuse technology is the next step in the technological evolution of modern aquaculture systems.
When compared to flow-through aquaculture systems, PRAS offer significant reductions in water consumption, effluent discharge volumes, and potentially energy consumption. Reuse technology allows for location of new facilities where there are limited water resources, and allows existing facilities to increase production despite limited water resources. With reduced water use, influent treatment and effluent treatment become more economical. As such, disinfection of influent water for biosecurity protection becomes possible and impact of the facility on the environment may be better mitigated. In addition to these benefits, water quality and temperature become easier to control which may have production benefits.
Partial Reuse Systems focus on the use of a few, simple treatment technologies to provide significant reductions in water use. These technologies typically include gas balancing and oxygenation, may also include solids removal and disinfection, but do not normally include ammonia removal through biofiltration. Those water quality parameters for which treatment is not provided are maintained within acceptable limits by flushing and replacement of a portion of the system water. Water temperature is dependant on influent water temperature which may be more economically altered than in a flow-through system due to the reduced flow.
Because flushing and water replacement is used to control the concentrations of some contaminants, the reuse rate is limited by the accumulation of untreated contaminants such as ammonia. The maximum reuse rate that may be achievable without the addition of more advanced treatment processes will depend on the biomass and feed load on the system, and on the specific water quality requirements of the fish cultured. Partial reuse rates from 50% to 90% of the total flow have been employed, depending primarily on fish sensitivity to unionized ammonia concentrations, although reuse rates between 50% and 75% are most common.
As reuse rates increase, the reduced exchange of system water may allow untreated contaminants such as ammonia and suspended solids to concentrate in the system. Recirculating Aquaculture Systems incorporate additional treatment processes to reduce the concentration of these contaminants, allowing for further water conservation through increased reuse rates.
Flow-through Aquaculture Systems
In traditional Flow-through Aquaculture Systems, water is passed through the culture system only once and is then discharged back to the aquatic environment. The flow of water through the culture system supplies oxygen to the fish and carries dissolved and suspended wastes out of the system. Water quality within the culture system is maintained by flushing of contaminants and by replacing all system water before dissolved oxygen concentrations drop below minimum acceptable limits or contaminate concentrations (i.e. ammonia, solids, and carbon dioxide) can accumulate to above maximum acceptable limits.
Although flow-through systems are predominantly constructed with raceway culture vessels, more and more facilities are being converted to use circular culture tanks which provide for more efficient use of water, superior mixing, superior removal of solid wastes, and the potential for increased fish densities.
Because flow through systems count on the exchange of water to flush contaminants from the system, high influent flow rates are required and equivalent high effluent flow rates are generated. Influent treatment and effluent treatment are often required to ensure that water quality is suitable and safe for fish culture or for discharge back to the environment. Because of the high flow rates, extensive treatments are often cost prohibitive and minimal environmental control is possible within the culture system. Temperature control is minimal and is often only possible through the use of systems that recover heat from the effluent flow.
PR Aqua offers a variety of products and services to meet the challenges that face many of today’s flow-through aquaculture facilities. Gas Balancing or oxygenation systems may be used to ensure that dissolved gas concentrations in influent water are appropriate for fish culture. Solids removal and disinfection systems may be used on influent systems to optimize water quality and prevent pathogen ingress, or on effluent systems to mitigate environmental impact. Monitoring equipment which can provide continuous evaluation of key water quality parameters will permit operators to adjust fish densities and feed rates to exactly match the carrying capacity of the culture water.
Flow-through systems became a popular and cost effective approach for aquaculture when water sources were plentiful and competing uses for the water resource were low. However, sustainability principles, increasing competition for limited supplies of high quality water, and the need for improved control of culture conditions are generally causing aquaculture facilities to consider partial reuse or recirculation technologies as alternatives to traditional methods.
Enclosed System: Locate Anywhere – Close to Markets
NaturalShrimp has spent many years developing and commercializing a technology that reliably produces a weekly crop of premium quality shrimp using a high degree of automation within an indoor environment. This proprietary production method minimizes labor costs, is completely eco-friendly and can produce fresh, gourmet grade shrimp in a high density environment on a commercial level anywhere in the world. The comprehensiveness, versatility and reliability of our control systems set us apart and make us the technology leader of the shrimp industry.
Vibrio Suppression Technology
Historically, efforts to raise shrimp in a high-density, closed system at the commercial level have met with either modest success or outright failure through “BioFloc Technology”. Infectious agents such as parasites, bacteria and viruses are the most damaging and most difficult to control. Bacterial infection can in some cases be combated through the use of antibiotics (although not always), and in general the use of antibiotics is considered undesirable and counter to “green” cultivation practices. Viruses can be even worse in that they are immune to antibiotics, and once introduced to a shrimp population viruses can wipe out entire farms and shrimp populations, even with intense probiotic applications.
NaturalShrimp’s primary weapon against infectious agents is its “Vibrio Suppression Technology”. This new innovative system creates higher sustainable densities, consistent production, improved growth and survival rates and improved food conversion without the use of antibiotics, probiotics or unhealthy anti-microbial chemicals. VST (Vibrio Suppression Technology) helps to exclude and suppress harmful organisms that usually destroy “BioFloc” and other enclosed technologies.
Automated Monitoring and Control system
The NaturalShrimp Automated Monitoring and Control system uses individual tank monitors as shown in the photograph to automatically control the feeding, the oxygenation, and the temperature of each of the facility tanks independently. In addition, a facility computer running custom software communicates with each of the controllers and performs additional data acquisition functions that can report back to a supervisory computer from anywhere in the world. These computer automated water controls optimize the growing conditions for the shrimp as they mature to harvest size providing a disease-resistant production environment.
Related news

Results in a green-water system show interactions with stocking density, natural food availability

Acute hepatopancreatic necrosis disease (AHPND) has caused substantial mortality in penaeid shrimp cultured in various countries in Southeast Asia.

India's production of vannamei shrimp is likely to drop in 2015, as farmers face disease issues and consider a shift to producing black tiger instead