Increase wine grape profits with successful mechanisation
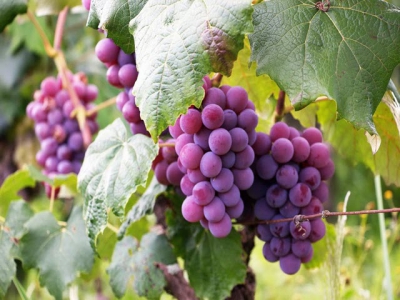
Izak de Beer may be one of only a few farmers in Olifantsriver in the Western Cape who is making a profit out of wine grapes. Creative use of mechanisation is one of the reasons for his success. Glenneis Kriel spoke to him about his production methods
Vines that are pruned mechanically become broader and much more vigorous than vines pruned by hand.
While most wine grape producers in the Olifantsriver have been struggling to keep their heads above water, Izak de Beer won the 2015 regional VinPro competition with a block of Colombar vines. His block yielded an income more than double the regional average. The 10,5ha block produced an average of 50t/ha at a cost of R30 000/ha and an income of R75 000/ha.
For 20 years, Izak kept his focus on quality. Then, last year, he shifted to profitability.
“People often think that mechanisation shortens the vineyard’s lifespan. My vineyards have proved that mechanisation can boost farm profitability without having a negative impact on vine health.
The judges found that the roots of the vines in the winning block grew right to the middle of the path between the planting rows, which meant they were more resilient than vines with roots mainly underneath a dripper,” he says.
Izak hesitates to talk about his secrets, not because he does not want fellow farmers to succeed, but because he has seen so many failures after sharing his formula.
“Farmers come and look at my set-up and are all ears while I explain my production recipe. Then, when they go home, they implement only those parts of the recipe that appeal to them. For example, they buy the expensive equipment, but skimp on fertilisation and irrigation. Then I get the blame when they pay the price for not doing it right,” he explains.
Izak identifies three factors that have been crucial to his success: economy of scale, the right equipment and adjusting production practices to accommodate higher yield from mechanisation.
Scale
Size matters in mechanisation. To justify the start-up cost in the Olifantsriver region, a farmer needs at least 50ha under production.
“It’s difficult to quantify exactly what size the area should be, as production conditions and profitability differ so much between farms and regions. The shrinking rand also makes it increasingly difficult for farmers to switch over. I bought a new tractor for R500 000 towards the end of last year; that tractor now costs about R750 000.”
The cost of entry, however, can be reduced in several ways.
“Farmers could buy machinery jointly and share it, or start with secondhand machinery. Alternatively, they could use contracters for pruning and harvesting or they could rent the equipment,” Izak suggests.
Equipment
Most of Izak’s machinery has been been customised to suit his needs. A complete switch to mechanisation makes the vines more vigorous and bulkier than hand-pruned vines. Since his production methods are based on Australian mechanisation methods, he uses the Ledgard pruning system.
The heavy-duty machine has two hydraulically powered cutter blades available in lengths between 0,8m and 2,4m. The 9mm cutter blade teeth can cut branches as thick as 32mm. This makes the machine suitable for summer and winter pruning.
While vines are traditionally hand-pruned to form 14 supporting branches with two buds each, mechanical pruners prune the vines into a ‘box’ in which each vine can have up to 200 buds. By contrast, hand-pruned vines have 56 buds at the most. Yield is thus far greater with mechanical pruners.
Since mechanised vines have the potential to get out of control, Izak may have to prune really extensively once in a while. For this, he uses a locally manufactured pruner fitted with iD-David blades from Spain. These are usually used to prune fruit trees and can cut branches with a diameter of up to 40mm.
Over the years, Izak has owned several harvesters, but he has finally settled on New Holland’s Braud machines. He is currently using a Braud 9090X.
“I like the Braud machines because they have a patented bucket that helps to prevent grapes from shaking out of the machine,” he says.
To accommodate the vigorous vines, the machine has been heightened to take 12 instead of seven rods. It has also been lengthened to prevent the grapes from shaking out of the back of the machine. The rods can be adjusted according to the height of the vines: for young vines, fewer rods are positioned at the bottom and for older vines more rods are added.
Izak has extended his mechanical creativity to other aspects of the operation. For example, he has developed a pole planter that utilises weights and counterweights. Last year, seven workers planted 600 poles in 20 days using this machine.
To counter the problem of snails, he uses two quadbikes fitted with fertiliser spreaders to put down snail pellets. Pellets are applied from two spreader pipes onto the vineyard rows at a rate of 5kg/ha. This is a major saving: 25kg/ ha are used if the pellets are broadcast by hand.
More water needed
Izak says that although his vines produce significantly more wine grapes than hand-pruned vines, the plants need more water and nutrients. “The leaf surface of my vines is about 30% greater than that in other vineyards in the region. This means my vines need a third more water and fertiliser. Because I only have enough water to irrigate 140ha of vineyards, I’ve capped production at 126ha so that I have water even during a dry year like this,” he says.
According to Izak, many of the region’s farmers have insufficient water to irrigate their vineyards.
“Farmers think they need to expand production to become more profitable, but if they don’t have the water to maintain what they already have, it can’t be done. So don’t expand or mechanise if you don’t have enough water to sustain increased production,” he warns.
His conservative water- use strategy should also help to pull him through the current dry season. Whereas most farmers in the region had run out of water by February, he still has enough to last until May.
“Vines have to be replenished after the harvest or you’ll pay for your neglect through reduced yield or vine losses,” he explains.
To supply more water, Izak uses 20mm pipes with a delivery rate of 3,6l of water an hour. The drippers are spaced 0,6m apart and the lines are raised about 50cm from the ground to prevent damage from implements. It is also easier to identify broken drippers when the lines are suspended.
Fewer vines/ha
Larger pipes mean that he can save energy by reducing pumping costs and he can also increase nutrient volume. He plants only 2 000 vines/ ha, in comparison with the region’s norm of 3 000 vines/ha, in order to reduce competition between the vines. Ramsey rootstock is used for most vine varieties, as it can support vigorous growth, is well adapted to the warm climatic conditions of the region, and is not susceptible to nematodes.
Richter is used for the red cultivars aimed at the higher quality market. The vines require a strong trellis system to support vigorous growth.
Izak uses a 1,5m-high, two wire cordon system with supporting wires at 50mm and 150mm from the top. Izak says that his main focus at present is on producing high grape volumes.“Producers in Australia are using techniques such as pruning their vineyards more severely and manipulating production by stressing the vines, to produce higher quality wines.
Related news

No-till may be a sustainable and cost-effective crop production system, but it comes with challenges of its own.

“The strawberries have been our saving grace this year,” says Mandy Aukamp of the Berrynice Berry Company near Molteno in the Eastern Cape.

Five Mpumalanga apple farmers have pooled their resources to establish their own packhouse, but each producer is independently responsible for producing