Hatchery environment matters for embryo development
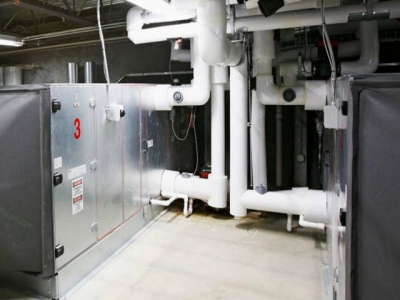
Air entering incubators must be preconditioned and then should be valued.
The optimum climate parameters for embryo development — temperature, humidity and the balance between oxygen supply and carbon dioxide release from the incubator — are the same, regardless of the climate zone in which a hatchery operates, up to an altitude of 1,200 m, according to Maciej Kolańczyk, senior hatchery specialist with Pas Reform Academy.
Developing embryos produce carbon dioxide and heat, he said, and moisture evaporates from the eggs. Much of the heat produced is collected by the water cooling system, and the rest is removed, together with the excess moisture and carbon dioxide, through ventilation. Used air is replaced by fresh air.
Kolańczyk noted that the purpose of ventilation is to provide fresh air and remove waste products. In addition, fresh air — which is usually drier and cooler than the air inside the incubator — lowers the humidity and absorbs some of the heat produced by the embryos. Ideally, the air exchange will be balanced so that the incubator's internal humidifiers, heaters and coolers simply have a corrective function and work only when necessary, he said.
Modern incubators are technically able to fully control their internal micro-climate. These systems are designed to maintain or restore the climate quickly after a machine has stopped or started or if climate parameters deviate from the set points.
It is preferable, however, not to have to activate the systems, because intensive heating, cooling or humidifying destabilizes the uniformity of the internal micro-climate, Kolańczyk reported, adding that it is a question of balancing the need for fresh air with the need to maintain a stable internal micro-climate.
If fresh air were taken directly from outside the building, its parameters would reflect the local conditions: the season and daily fluctuations in temperature and humidity. Even in a moderate climate zone, temperatures can vary by up to 50°C throughout the year, and daytime and nighttime temperatures can fluctuate by 20-30°C. Likewise, humidity can vary substantially over 24 hours, depending on the weather conditions.
According to Kolańczyk, these fluctuations in the fresh air parameters represent a challenge for incubators. In order to achieve the desired set points, intensive heating, cooling and humidifying would have to take place, but this would reduce the uniformity of conditions inside the cabinet, he added.
To overcome this problem, air entering the incubator must be preconditioned. The optimum temperature range is 21-27°C, with a relative humidity range of 50-60%, he noted. Creating these stable parameters requires an air handling unit (AHU). Preconditioning is a costly process, and therefore, prepared air should be valued, he said.
In practice, Kolańczyk said to lower the influence of outside climate conditions, fresh air comes either from a room inside the hatchery building or a specialized air preparation room that can supply preconditioned air hygienically and economically. The air in either of these places should be seen as a precious resource that must not be wasted. It should be carefully stored and protected, and only the necessary amount should be used, he added.
A hatchery setter with space for 100,000 eggs needs an average of 400-500 cu. m of fresh air per hour, Kolańczyk said, so a hatchery with many incubators will need a multiple of this amount of fresh air.
Kolańczyk suggested the following key points of advice:
Make sure the capacity of the AHU is sufficient for a hatchery's incubators.
Maintenance of the AHU is important, so keep filters clean and dry, and check motors and mechanical parts regularly.
Do not waste air that has been preconditioned to the optimum parameters. Keep all hatchery doors closed.
Use carbon dioxide controllers to monitor the ventilation rate. Make sure incubators take only as much air as is really necessary to keep the air fresh enough.
Related news

Managing the moisture content in feed formulations is critical as it can compensate for weight losses during feed processing, it can also preserve the shelf

The SMART Broiler program will develop tools to quantitatively assess and collect information regarding key welfare indicators such as walking ability

Some of these variations may alter the IFITM proteins, suggesting that they could have functional consequences and may affect the ability of chickens to fight