Commercial implementation of in-pond raceway system
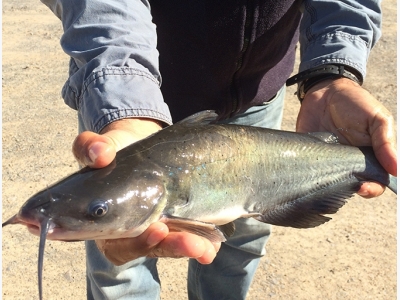
Catfish farmers effectively supply niche markets
Hybrid catfish have been raised in an in-pond raceway system to supply niche markets
Most commercial catfish farmers in the southeastern USA sell their catfish directly to a processing plant. Unfortunately, due to fluctuations in the supply and demand for catfish, prices have typically not kept up with production costs and often fluctuate widely. Competition from foreign imports has compounded the problem by keeping the wholesale price of catfish down, leading to lower prices for live fish. In order to obtain a higher price for their product, one farm in Alabama has developed an alternative niche live market for catfish within the Asian grocery store community and is supplying it exclusively with hybrid catfish (Ictalurus punctatus x Ictalurus furcatus) produced in an in-pond raceway system (IPRS).
For two production seasons at Weissinger Lakes (Browns, Ala., USA), catfish produced in the IPRS have been sold weekly to Asian markets located in multiple states (Fig. 1). In 2012-2013, more than half of the fish produced in the IPRS were sold to niche live markets while the rest were sold to large-scale processors. In the following year (2013-2014), the market expanded to also include recreational lake and pond stocking. The fish produced in the IPRS were exclusively sold to the niche markets at a higher price than would have been obtained if selling to a processor.
The design of the IPRS makes harvest of small amounts of fish (<450 kg weekly) feasible from the standpoint of labor, time, and cost. Since fish are confined to raceway cells that are easily crowded and harvested, a significant reduction in labor cost has occurred compared to harvesting larger traditional levee ponds. This has made it economically feasible to harvest small amounts of fish on a weekly basis. The farm originally developed the niche market for tilapia that were being raised in an indoor recirculating facility and later began supplying the same market with catfish. Wholesale meat and fish companies have indicated that “one stop shopping” for a variety of fish products from a single producer is desirable. In addition, some of the catfish have been sold for use in pay-out lakes (fee fishing) and for stocking in private recreational fishing ponds, also at prices higher than would have been obtained by selling directly to a processor.
In-pond raceway systems are considered intensive production, allowing for both large and small scale marketing of catfish. Large scale marketing in west Alabama typically involves selling catfish to processing plants in large quantities on a year round basis. Fish within individual raceway cells can be harvested on a weekly basis and sold to niche markets. This has often enabled the producer to obtain a higher price compared to the processing plant.
Hybrid catfish being loaded out for stocking of private ponds and lakes
In-pond raceway system
For the last two production cycles, hybrid catfish fingerlings were stocked in an IPRS in Browns, Ala., USA (Fig. 2). The IPRS is housed in a 2.43 ha earthen pond with an average depth of 1.7 m supplied by well water and watershed runoff. The IPRS consists of six, individual raceways that share common walls and are attached to a permanent concrete foundation and represents 3.7 percent of the total pond area. Fish were confined in culture units (45.9 m3) by end partition barriers that spanned the width of each raceway unit. Water flow into the raceways was aided by a rotating paddle wheel and was exchanged in each raceway approximately every five minutes. Water flowed from raceway units into the north side of the pond, moved counterclockwise to the south side of the pond, and returned to the inflow side of the raceways. A central baffle wall extended from the raceways into the pond to assure water recirculated in a long pathway. A regenerative blower equipped with a diffuser grid was operated when dissolved oxygen concentrations fell below desirable levels in raceway units.
View (to scale) of the in-pond raceway system used to supply niche markets in Browns, Alabama.
Fingerling hybrid catfish were obtained from a commercial supplier (Need More Fisheries, Glen Allan, Miss., USA). Hybrid catfish (45 – 222 g) were stocked separately into raceways in 2012 (production cycle 1) and 2013 (production cycle 2), at densities of 9,727 – 12,778 fish per raceway (and in one case during production cycle 2 at 30,194 fish in one individual raceway). During production cycle 1, four raceways were selected for the trial. Two of the raceways were utilized to supply niche markets, while catfish from the other two raceways were sold directly to the processor. Three of the four raceways were stocked with large stocker sized fish and the remaining raceway was stocked with fingerlings. Following positive results from production cycle 1 and expansion of the farmer’s market, during production cycle 2 five raceways were utilized to produce fish exclusively for various niche markets.
The grow-out phase was conducted for 10-19 months depending on size of fish initially stocked and stocking densities of the raceways. Fish were fed a commercial, floating feed (32 percent protein, Alabama Feed Mill, Uniontown, Ala., USA) 2 – 4 times per day based on biomass, water temperature, and fish size. Catfish were harvested throughout the study as they reached marketable size (Fig. 3 & Fig. 4). Due to the ease of harvest, a range of sizes were sold based on customer demands.
Partial harvest of an in-pond raceway in Browns, Alabama.
Results
Results from the first production cycle were very promising. Survivals ranged from 75-92 percent for the four raceways that were stocked. All fish were harvested between 10-12 months following stocking. Net yields and FCRs ranged from 3,550 to 5,730 kg/raceway and 1.25 to 2.49, respectively. During the first production cycle, fish from raceways 2 and 4 were sold to the processing plant at an average price of $1.87/kg, while fish from raceways 1 and 3 were sold to niche Asian markets throughout the southeastern US at an average price of $2.14/kg.
During the second production cycle, several incidences of disease occurred in the IPRS, including virulent Aeromonas hydrophila, enteric septicemia of catfish, and columnaris. This drastically reduced survival (31-57 percent) and profitability during production cycle 2 (Tables 1 and 2). In fact, the farm lost money on four of the five raceways during the second production cycle. It is also worth noting that the length of the production period for cycle 2 was much longer (12-19 months) compared to production cycle 1 (10-12 months). The IPRS possesses several advantages over traditional pond production systems, including ease of treatment with chemicals during disease events and better inventory control (individual dead fish can be counted). Nevertheless, incidences of disease in the smaller confined fish culture area of the IPRS can be problematic and in some cases catastrophic. It is possible that the increased partial harvesting activities (crowding of the raceway during harvest) increased scrapes, cuts and punctures to remaining fish and thus increased the ease of bacterial disease entry into the catfish. During production cycle 2 all sales were to small live markets, recreational pond stocking, and fee fishing operations, resulting in a price range of $2.20-$3.85/kg. This range in price depended on whether or not the fish were picked up on site by the customer or delivered by Weissinger Lakes.
RW-1 | RW-2 | RW-3 | RW-4 | |
Production Period (mo) | 12 | 10 | 11 | 10 |
Cycle start/end dates | 6/2012 to 6/2013 | 6/2012 to 4/2013 | 6/2012 to 5/2013 | 6/2012 to 4/2013 |
Weight stocked (kg)/RW | 2,200 | 2,236 | 653 | 2,041 |
Head stocked/RW | 12,570 | 12,778 | 12,424 | 11,664 |
Average weight at stocking (g) | 175 | 175 | 49 | 175 |
Total harvested (kg/RW) | 0.6 | 0.7 | 0.4 | 0.7 |
Average weight at harvest (kg) | 3,350 | 5,257 | 4,418 | 5,730 |
Net yield (kg/RW) | ||||
Survival (%) | 75 | 86 | 95 | 92 |
Total feed feed (kg/RW) | 8,832 | 9.397 | 5,482 | 9,028 |
RW-1 | RW-2 | RW-3 | RW-4 | RW-6 | |
Production Period (mo) | 19 | 19 | 12 | 19 | 16 |
Cycle start/end dates | 6/2013 to 1/2015 | 6/2013 to 1/2015 | 6/2013 to 6/2014 | 6/2013 to 1/2015 | 6/2013 to 10/2014 |
Weight stocked (kg)/RW | 769 | 613 | 689 | 1,902 | 755 |
Head stocked/RW | 12,209 | 9,727 | 10,937 | 30,194 | 11,977 |
Average weight at stocking (g) | 63 | 63 | 63 | 63 | 63 |
Total harvested (kg/RW) | 3,100 | 3,284 | 3,161 | 7,551 | 2,685 |
Average weight at harvest (kg) | 0.6 | 0.6 | 0.5 | 0.5 | 0.7 |
Net yield (kg/RW) | 2,331 | 2,671 | 2,472 | 5,649 | 1,930 |
Survival (%) | 44 | 57 | 57 | 48 | 31 |
Total feed feed (kg/RW) | 5,874 | 5,972 | 6,311 | 11,032 | 7,511 |
Perspectives
In-pond raceways can be effective culture systems for supplying niche markets with fresh fish in the US and elsewhere. The large size of most traditional catfish ponds in the US (> 3 ha) makes partial harvest for small amounts of fish not practical, time consuming, labor intensive, and costly. The cost of a weekly harvest of catfish from the IPRS including labor and cost of diesel fuel to run the boom truck was $25.50 and can be accomplished in approximately 30-45 minutes. The harvest of small amounts of fish on a weekly basis from an IPRS is a means whereby small scale producers can achieve a higher price for their product by targeting niche markets. Despite the promise of IPRS for supplying niche markets, further research is needed on these systems to reduce disease related mortality in catfish. Specifically, improved protocols for managing fish health in intensive raceway systems with numerous partial harvests needs to be investigated and developed to take advantage of live fish niche marketing opportunities using this production system.
Related news

Tilapia culture has been practiced in Egypt since the beginning of recorded history. Aquaculture research started in the 1930s, while modern commercial tilapia

Experience raising tilapia in biofloc technology (BFT), where aerial feeding rates are at least four to five orders of magnitude greater than in shrimp BFT

Biofloc technology (BFT) is a new aquaculture practice currently revolutionizing the shrimp farming sector in Asia and South America.